Scandinavian Freehand Pipes
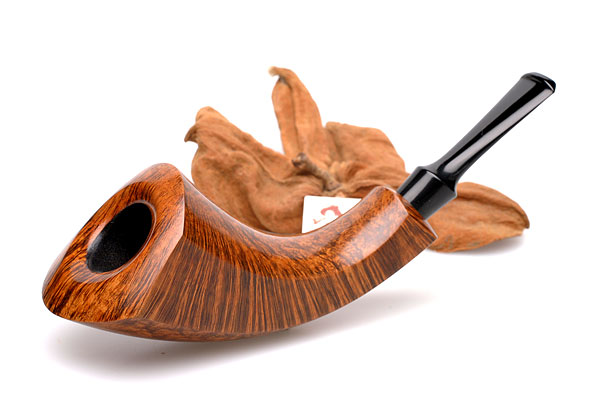
Bo Nordh
Introduction
This article is an attempt to write a short history of the origins and development of the Scandinavian freehand pipe. Some parts – in particular the classification of pipe makers into schools and workshops – are based on an article by Jakob Groth, and are used with kind permission of the original author, who for many years worked at the legendary “Pibe Dan” shop.
The purpose of this article is to give a general overview of the circumstances under which this special “pipe scene” developed, and to present the main people involved. Pipe smokers will get background information on pipes they own or might be interested in. This presentation does not pretend to be complete, so useful comments are encouraged and will be received with thanks.
To define the subject of this article, the pipe maker, the following will be used: A pipe maker is an artisan who makes pipes from start to finish. The produced pipe is the product of one person only; this person takes care of the whole production process, from design to finish. Furthermore he shapes his pipes by hand and handcuts his mouthpieces, which means he is not using contour milling or pre-molded mouthpieces.
To recognize the innovation involved in the creation of the Scandinavian freehand pipe, let us recapitulate the three general ways to produce a pipe bowl.
1) Contour milling is used to produce a series of identical pipe bowls by using a master bowl. This method is normally used by pipe factories. 2) The pipe maker uses a lathe to raw-turn the bowl, which normally results in spherical bowls and shanks. Then, the intersection between bowl and shank is worked on with an abrasive belt grinder. 3) The pipe bowl is held against a sanding disc and thus, shaped freehand. This technique allows the pipe maker to create, among other things, asymmetrical shapes.
In the 1950s, Sixten Ivarsson developed pipe shapes that are today known under the label „Danish Classic“. At the same time he started collaborating with Stanwell.
Stanwell was the only Danish pipe factory established in the war years which survived the reintroduction of English pipes onto Denmark’s market. Although their pipes are produced in a factory, we will come back to Stanwell. Sixten was always willing to share his ideas. Many of Stanwell’s modern shapes from the 1950s and 1960s are based on his designs. Thus, Danish pipe design became popular throughout the world – comparable to the success of Danish designed basic commodities in these years (see Gert Holbek).
The 1960s saw the breakthrough of Danish pipes. There was an enormous export growth for factory-made pipes as well as unique copies from pipe makers, which helped many Danish pipe makers to establish their own workshops. Many of them even became schools for specific designs that are known to this day. Thus, it is still possible, by recognizing characteristic features of a pipe, to know which school its maker belongs to.
Sixten Ivarsson and His School of Pipe Making
There is a general consensus that the history of Scandinavian Pipe Making starts with a Swede: during World War II, Sixten Ivarsson (1910 – 2001) lived as a debt-collector in Copenhagen.
When he broke the shank of his pipe, he brought it to a then well-known workshop – Suhrs Pibemageri (Teofil Suhr’s pipe workshop in Copenhagen). Sadly, the responsible repairman was ill, so Sixten had to fix it himself. Seeing his skillfully executed repair, he was offered a job on the spot. Because the supply of new pipes had been cut short by the war, Sixten was overwhelmed with work. Thus, he learned a lot about how pipes were made, and – probably even more important – how they should not be made.
After the War imported briar became available again, and Sixten began to experiment with making his own pipes along besides his job. Since it was still not possible to get the desired English briar pipes, Sixten was able to sell his pipes even though they were 5 to 10 times more expensive than the Danish factory pipes.
Sixten Ivarsson began experimenting with new shapes at the end of the 1940s and the beginning of the 1950s. Before, most pipes were shaped in the classic way, and the few exceptions were not very harmoniously designed. Sixten was the first one to refine these shapes, and eventually created the so-called freehand pipe.
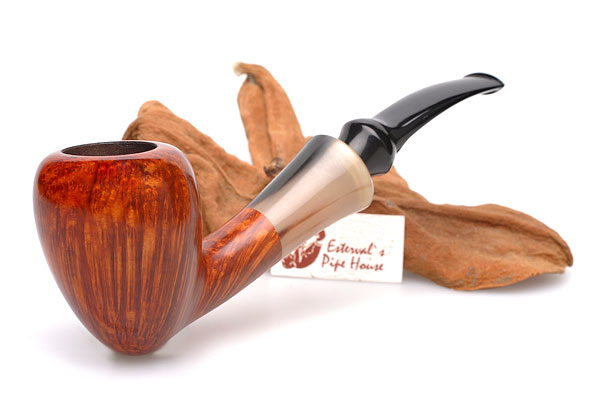
Sixten Ivarsson
Many of his pipes had a “drop” on the bottom side of the bowl, which made them look like an egg.
He also set a new standard in terms of craftsmanship. Today a handmade pipe is expected to have a perfectly aligned bore, comfortable bit, smoothly finished bowl and mouthpiece, and nice grain. But at that time even most factory-made pipes were more or less imperfect. Sixten also raised the technical production quality.
Sixten also began using applications made of materials like bamboo, horn, or even cattle bone with an elegance that had never been seen before. Because briar wood was scarce after the end of World War II, Sixten had to be creative. As legend has it, Sixten was able to make three pipes out of a briar block which was used for a single one by a “normal” pipe maker. This efficiency was achieved by cutting out pipes whose shanks were too short and, thus, had to be extended with another material later.
Sixten was born in 1910 and passed away in 2001. He produced his last pipes in 1992/3, and had never created more than 200 pipes per year, which were sold in many countries of the world, for example Japan, Denmark, Germany and the United States, to name just a few. Sixten stopped grading his pipes in 1965.

Jess Chonowitsch
Besides being the first great pipe maker according to the above-mentioned definition, Sixten also was a very good teacher. One of Sixten's mottoes was, "It is a bad teacher who does not allow his student to become better than himself." Some pipe makers have directly had the pleasure to be taught by Sixten, while many more were inspired by his work. Pipe makers who were taught or guided by Sixten include prominent names like: his son Lars Ivarsson, Jorn Micke, Jess Chonowitsch, and Bo Nordh, but also Hiroyuki Tokutomi and other Japanese pipe makers, as well as his granddaughter Nanna Ivarsson of course.
Typical for the Sixten school of pipe making was an emphasis on quality workmanship. All details had to be done with a high degree of perfection. It was very important to Sixten that the pipes were good smoking instruments – even though the shapes of the pipes are more sculptural than in the other schools. Many of these pipes can be considered as the work of a sculptor trying to make the most of the briar as an interesting material. This means that many pipe shapes are asymmetric, and have soft and flowing shapes. They are often finished in various shades of brown.
Poul Rasmussen and His School of Pipe Making
Poul Rasmussen was the second pipe maker in Denmark. He was the foreman in Suhr's pipe workshop after Sixten had left. Suhr's had to repair a lot of pipes! Later, Rasmussen established his own workshop in Hornemannsgade.
He rarely stamped his pipes with his name. It is also obscure whether the red-white dot, which is being used by Anne Julie today, was the original symbol for Suhr’s, which some pipes suggest; or whether it was the symbol used by Poul Rasmussen himself. One thing is clear though: while playful and flowing shapes were being developed in Sixten Ivarsson’s school in the 1960s, Poul Rasmussen’s pipes kept a classic look.
There are many classic shapes that are not far from factory-made ones, the only differences being their slimness and slightly slanting bowls.
This school also significantly developed the contrast stain, originally introduced by Sixten Ivarsson, which is used to accentuate the briar’s grain
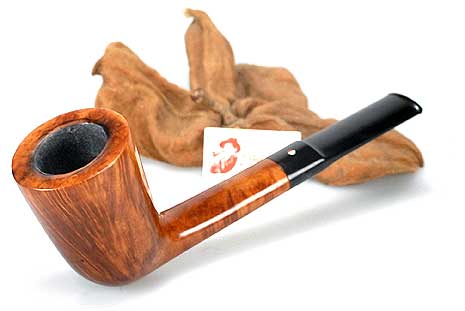
Poul Rasmussen
When Poul Rasmussen died due to cardiac insufficiency in 1967, one of his pupils wrote: "His biggest importance for the future of Danish handmade pipes is that from his workshop have come many of our most skilled pipe artists, who can thank Poul Rasmussen for their knowledge and ability. They now work individually on the basis he created." Some names to be mentioned from this school are Emil Chonowitsch, Jess Chonowitsch, Bjorn Bengtsson, Tom Eltang, and of course Anne Julie, the widow of Poul Rasmussen.
Jess Chonowith is the only well-known pipe maker who was taught in both schools, at first Poul Rasmussen’s and then Sixten Ivarsson’s.
The Workshop of W.O. Larsen and Other Workshops Affiliated with Stores
W.O. Larsen, Denmark's oldest and probably most famous pipe and tobacco store, is located in the center of Copenhagen, on the main pedestrian street called Stroget (although its streets have completely different names). In the beginning of the 1960s the store had begun to sell Danish handmade pipes, especially from Poul Rasmussen. They sold so well that Poul Rasmussen could not keep up with the demand. Thus, W.O. Larsen – with their dynamic business manager Svend Bang – decided to establish their own workshop next to the store.
The first manager of the pipe shop was Svend Knudsen, but he soon left to make pipes under his own name. Hans Nielsen, also known as "Former" – named after the late British actor George Formby, with whom he had some similarity – was its next manager. Under his management the workshop grew and W.O. Larsen pipes became well-known abroad. Among the prominent pipe makers educated there are: Else Larsen (Denmark's first female pipe maker), Poul Ilsted, Ph. Vigen, Teddy Knudsen, Tonni Nielsen, Peter Hedegaard, Bennie Jörgensen, and Sören Refbjerg.
Semi-classic shapes are typical for the W.O. Larsen school. This means that classic shapes are slightly changed, often by making them appear more full or round. The pipes often have lower point of gravity. This means that a typical billiard would have a bowl shaped more like a pear and the connection between the bowl and the shank would be clearly distinguishable. Yellow and orange are commonly used colors for the finish.
Another workshop that has to be mentioned here is Pibe-Dan (Pipe-Dan), which unfortunately had to close in 1991. Pipe-Dan was the Mekka for aficionados of handmade pipes, and offered many of the leading Danish pipe makers’ products. A number of now-famous pipe makers sold their creations there (for example Gert Holbek and Björn of Sweden.)
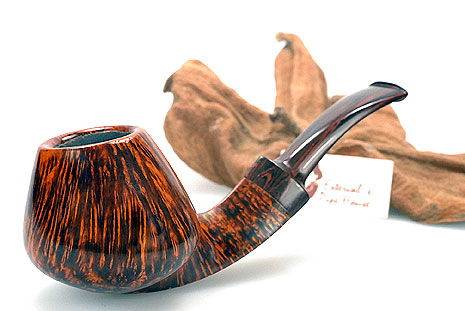
Phil Vigen
Pibe-Dan would always let the pipe maker stamp his own name on a pipe along with the shop’s name. They had a workshop too, but it mostly did repair work. One of their lines of pipes was called "shape reformed", which meant that a traditional shape had been redesigned. Some of the Pibe-Dan pipes were carved by Tom Eltang and Ph. Vigen.
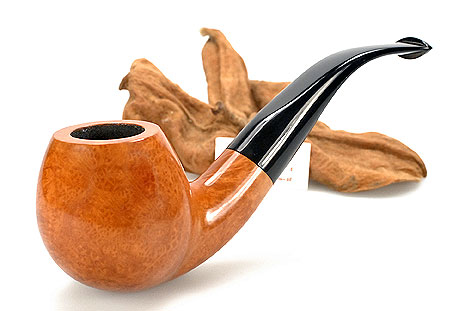
Hans Hartmann
Yet another workshop with a very good reputation in the 1960s was the one of Hans Hartmann, though it never generated a school. The most famous pipe maker who was inspired by Hans Hartmann in his early years is Per Hansen (Bang).
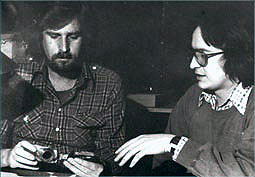
Preben Holm mit Poul Winslow
Besides these important workshops, many pipe factories were established. Danish design had acquired a good reputation, and in the less expensive lines a lot of semi-handcut freehand and fancy pipes were sold. Because pipe makers rode the popularity wave of fancy pipes for too long, they today are looked at with chagrin by many. Their protagonists were Preben Holm, Karl-Erik, and Erik Nörding. All three survived this trend, because they had the ability to change their shaping when the market for fancy pipes finally shrunk and higher quality was demanded.
Bang - Pipes
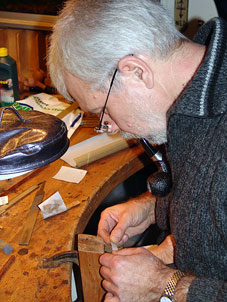
Ulf Noltensmeier
The name Bang pipes is a bit of a paradox, because it does not denote the name of an individual pipe maker. Before starting his own business in 1968, Svend Bang had already gained a lot of experience in the pipe and tobacco world as W.O. Larsen’s business manager in Copenhagen.
It is considered quite unlikely that Bang himself has ever made any pipes, although it is said that the unsmoked “Löfberg” pipes which emerged in Germany a few years were allegedly made by him.
The current trademark owners do not only keep quiet about this incident, but also on the complete list of pipe makers who have ever worked for Svend Bang – although certain design characteristics and gradings suggest a number of them. Ivan Horst Nielsen mentions Rafn as Bang’s first pipe maker. In addition, Jan Wiedelöv, a personal acquaintance of the author, and Ph. Vigen have definitely worked for Bang.
It is beyond dispute though, that Per Hansen began to work for Bang in 1970; Ulf Noltensmeier followed in 1971. Before joining Bang, Hansen had for a short time worked with Preben Holm, Noltensmeier, and Anne Julie. For over 35 years, these two pipe makers are responsible for Bang pipes. After his retirement in 1984, Svend Bang sold the company to Per and Ulf.
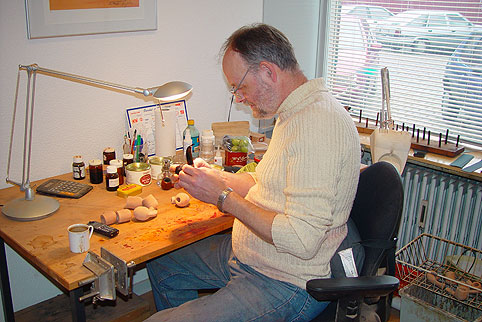
Per Hansen
Knowing the working style and workshops of many Scandinavian pipe makers, you quickly realize that Bang is different in many ways. While almost all other pipe makers work individually, Per and Ulf work as a team, though each one of them has his distinctive style. Their modern workshop is still situated in an office building in the city of Copenhagen, while many other pipe makers prefer to live in a farmhouse in the countryside or near the sea. In contrast, Per and Ulf have their 9-to-5 job in the city.
Until some years ago, Per’s pipes often were curved and sculptural, while Ulf’s appeared more classic in shape. But this has changed over the years and today it can be quite difficult to recognize who has been responsible for a specific pipe. Both say that they have been inspired by some of the old masters, but what they really benefit from is their efficient co-operation. Together they have developed a number of shapes and lines, and have created some of the world’s most beautiful pipes. They sell their pipes to Germany, Switzerland, Austria, Italy, USA, Taiwan and Japan. Because each one of them creates only about 200 pieces per year, the demand can not be met.
Sandblasted pipes are a specialty of Bang. While other pipe makers often outsource the sandblasting to Stanwell, they do it themselves. Their sandblasted pipes usually have a very deep texture and a distinctive and beautiful grain. The silver work on the pipes is quite unique as well. They not only produce silver bands, but also wind caps. Fit and finish of the pipes are absolutely perfect, and the mouthpieces are exceptionally black and shiny.
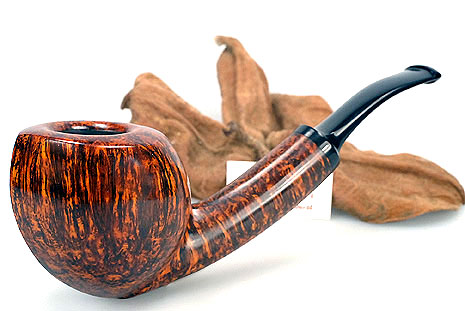
Svend Bang
Bangs’s grading is based on a system introduced by Svend Bang in 1970. Since 1984, the year the company was sold to the pipe makers, they are stamped “S. Bang København” and graded: black sand, tan sand, 5 – 9 and A – B. Only unique pieces are individually numbered and often stamped with the actual pipe maker’s initials (PH for Per Hansen or UN for Ulf Noltensmeier).
Gert Holbek
Gert Holbek is probably the oldest Danish pipe maker – after the death of Sixten Ivarsson –, since he was born in 1928. He is for sure the oldest active pipe maker and definitely the one who has been in the business for the longest time: he started with Poul Rasmussen in 1953. After 1½ years and more than ten thousand pipe repairs, he opened his own workshop and has made pipes ever since.
For a number of years he produced about two hundred pipes per year, which were all sold through Pibe Dan, until the shop closed in 1991. Pibe Dan’s English catalogues from the 1960s made his name famous in Europe, Japan, and the United States. In the last years the number of pipes produced has decreased considerably, but he still can not a resist the appeal of a beautiful briar block. The few pipes he creates are almost exclusively sold to Japan, where he has had devoted customers for many years.
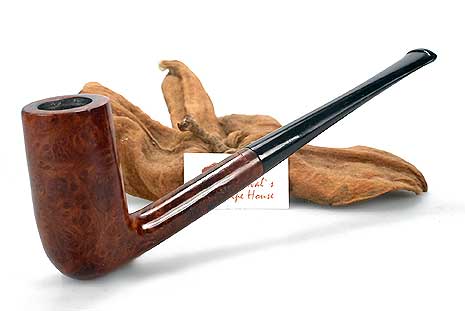
Pipe-Dan Copenhagen Shape Reformed 20 433 Estate
Although Gert has been in the pipe business for 50 years, he is not very known among pipe smokers and collectors. Probably because he never wanted to be a part of the “pipe scene”, and, thus, Danish pipe magazines never featured him in any of their articles. Only the old regular customers of Pibe Dan recognize his name with appreciation. For a period of time he engaged in industrial design and technical innovations. His sense of form and idiom can be recognized in a set of knife, fork and spoon, called Prism, which he designed in collaboration with a childhood friend in the beginning of the 1960s. The set is still sold in large quantities all over the world. He also owns several patents, and has “invented” 2211, which is probably the best cleaning fluid for pipes, because it dissolves the residue, disinfects the pipe, and impregnates the smoking channel.
The distinct pipe designs of Gert Holbek have hardly changed over the years and can be recognized quite easily. Not much tells you that he originally started with Poul Rasmussen, perhaps only that many of his pipes have rather tall and slender bowls. His tall pipes, called chimneys, were created in collaboration with Pibe Dan. His pipes are almost “ascetic” (this is the word he uses). You will never find a ring, a ferrule or any decoration on a Holbek pipe. His shapes have soft, but springy lines with smooth passages between bowl and shank, and bowl’s rim is concave more often than not. His smooth pipes are mostly straight grain and come in a warm reddish walnut finish. The probably most characteristic feature lies in the fact that Holbek grinds the edges of the bit slantingly.
Stanwell
Talking about Danish Pipes, you can not underestimate the importance of Stanwell. Contrary to expectations, there is little contradiction between the factory-made pipes of Stanwell and the handmades from individual pipe makers. Rather, they describe two sides of the creative Danish pipe environment, in which each side gains from the other. Early in the 1950s, Poul Nielsen Stanwell started to collaborate with Sixten Ivarsson. Poul Nielsen Stanwell had realized that he had to offer more than traditional (English) shapes if the company was to survive. Therefore, Stanwell introduced several of the new Ivarsson shapes into series production, many of which are still available today. Later, other pipe makers contributed their designs to Stanwell.
The 50th Anniversary Jubilee set of 6 pipes from Stanwell is a tribute to Danish pipe makers. The set includes one bulldog (Stanwell’s first pipe from the 1940s), and five pipes created by masters of Danish pipe making: Sixten Ivarsson (2), Jess Chonowitsch, Anne Julie, and Tom Eltang. Even today this style of cooperation is fruitful. Many new Stanwell shapes are created by pipe makers, while some of them have their own pipes sandblasted on Stanwell's machinery, and are allowed to pick particularly beautiful pieces of bamboo or even plateau briar blocks from Stanwell’s supply.
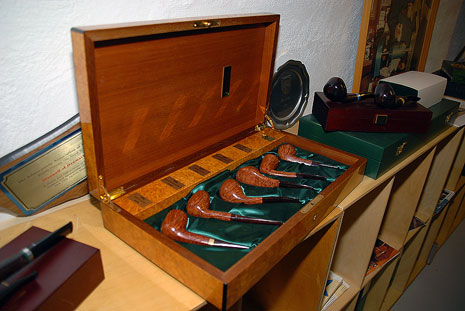
Das Original 6er Set, erstellt von Anne Julie
The mid 1970s saw the end of larger workshops. Sixten Ivarsson was getting too old to have pupils, and Anne Julie preferred to run the workshop alone. W.O. Larsen closed the workshop and instead contracted to buy straight grain hand made pipes from individual pipe makers and then stamped them with the company’s name. Even a lot of factory made pipes and semi-hand cuts were sold under the W.O. Larsen name. The pipe makers that have emerged since then have studied with one pipe maker or worked in a pipe factory, and became independent sooner or later. Through “learning by doing” they developed their own style.
Copyright © 2007 by TECON GmbH
with friendly support of Jörg Lehmann |